Digitalização com normas abertas: a receita para a tranquilidade
Publicado às 02 de setembro de 2024 em Operational Excellence
Estas são algumas das preocupações que inquietam os gestores de fábrica e que podem ser resolvidas através da digitalização. Num ambiente de produção digitalizado, os gestores de fábrica não têm de se preocupar com as incógnitas, os riscos e as possibilidades. A digitalização elimina a incerteza e permite a otimização orientada pelo desempenho. Fornece informações que podem ajudar os gestores de fábrica a melhorar a qualidade, reduzir custos, encurtar os tempos de processo e diminuir o impacto ambiental. O gestor de uma fábrica digitalizada não deve ter preocupações à noite, mas, se tiver, bastará olhar rapidamente para o telemóvel para ter a certeza de que tudo está a funcionar em condições.
No entanto, passar de um estado de insónia provocada por ansiedade para um sono tranquilo não é fácil. Na verdade, a digitalização pode ser bastante entediante. Os líderes de projeto raramente têm o luxo de trabalhar com uma tela em branco; na maioria das vezes, trabalham com uma "manta de retalhos" de antigas tecnologias combinadas; tentam digitalizar linhas de produção incorporando máquinas que nunca registaram dados e foram construídas antes mesmo da existência dos protocolos de comunicação. Tudo isto contribui para um desafio considerável de integração de TO e TI.
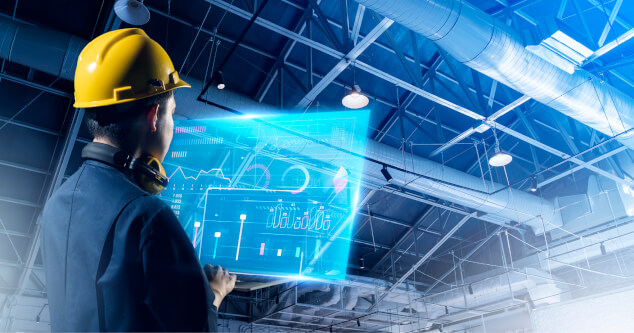
Ter como objetivo 80%
Pode utilizar normas não abertas, mas, em última análise, isto irá limitar a sua capacidade de tirar o máximo partido das oportunidades de otimização de desempenho que a digitalização apresenta e de comunicar para além das paredes da fábrica, razão pela qual defendemos uma abordagem de digitalização de norma aberta.
Para recolher dados de máquinas e processos em tempo real, uma linguagem de modelagem comum, como a PackML, alcançará a uniformização. A digitalização bem-sucedida também requer um protocolo de comunicação padronizado para que as máquinas possam comunicar umas com as outras e com outros componentes da Indústria 4.0. O OPC UA, um protocolo que tem origem no domínio de TI, está cada vez mais a entrar na esfera da automação industrial, e a OMRON faz parte de um comité de direção orientado pela indústria da automação, que está a alargar o OPC UA a dispositivos industriais ao nível do terreno, denominados UPC UA FX.
A analogia que utilizo frequentemente é com a língua inglesa, a língua universal dos negócios. Se falar inglês, pode fazer negócios com a maioria das pessoas. O mesmo princípio aplica-se ao OPC UA FX num contexto industrial.
Esta norma aberta suporta a total interoperabilidade dentro de uma fábrica. Não só permite que as máquinas comuniquem entre si em termos de dados, como também permite que as máquinas comuniquem com sistemas de TI, como os sistemas ERP e MES, bem como com sistemas de análise de dados que possa estar a executar numa nuvem local ou virtual.
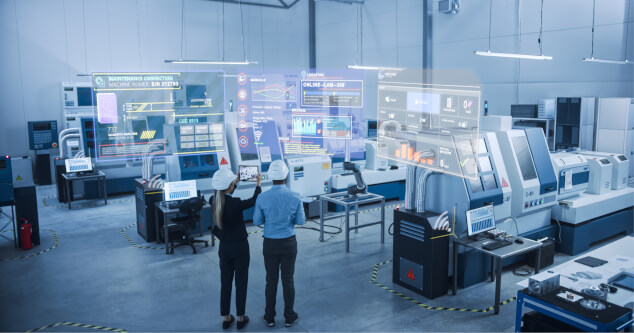
Criação de oportunidades
A digitalização de norma aberta também é essencial para obter valor dos Passaportes de Produtos digitais (DPP). Além de serem um requisito legal de 2027 para algumas indústrias, os DPP, que fornecem um registo digital da composição, da origem e do ciclo de vida de um produto, são uma ferramenta útil da Indústria 4.0. Na produção de baterias para veículos elétricos, por exemplo, os DPP podem ser utilizados para melhorar a qualidade e reduzir o desperdício. Verificou-se que a combinação de componentes da mesma qualidade resulta numa melhor bateria. O motivo pelo qual nem sempre acontece é a variação que ocorre dentro das tolerâncias definidas. Ao utilizarem dados dos DPP comunicados através do OPC UA, os armazéns podem escolher componentes individuais com características semelhantes e, por conseguinte, reduzir o risco de as baterias falharem nos testes de fábrica e terem de ser eliminadas.
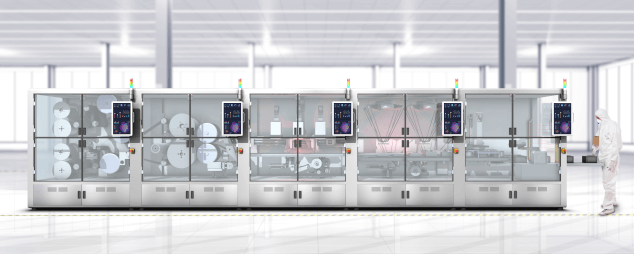
A digitalização está a ganhar ímpeto com a crescente consciencialização sobre as vantagens reais que as informações orientadas por dados podem trazer. No entanto, a uniformização, quanto ao tipo de dados a recolher e a forma como estes dados são comunicados, constitui um grande desafio para as fábricas que pretendem digitalizar a automação industrial. Ao adotar uma abordagem de norma aberta, os fabricantes podem ter sucesso na digitalização e os gestores de fábrica podem desfrutar de tranquilidade.